A shunter's lament
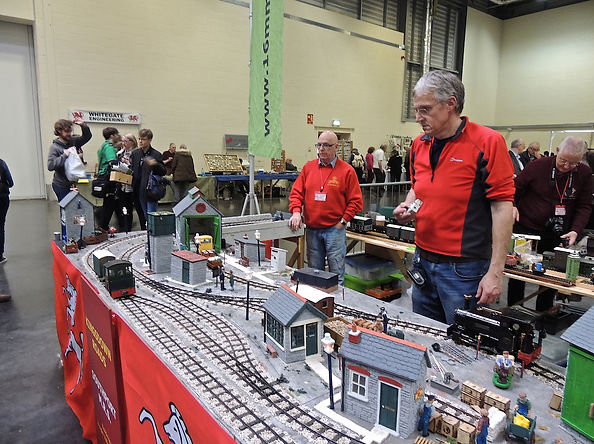.jpg)
If you have two 16mm layouts in your garage, the need for a third is perhaps not immediately obvious. However there was one factor making the need for expansion if not urgent then certainly worth pursuing. The existing pair are fairly large constructions, requiring multiple attendants and transporter vehicles for deployment. I wanted something that could be moved, set up and operated with just a couple of operators, and perhaps a third as relief.
I also wanted to make more use of three steam locos fitted with Slomo units. They were intended for the turntables on Middleforth, a 24ft end-to-end layout I built for the West Lancashire Light Railway. These engines performed well in that situation, but their ability to crawl at scale speeds make them also useful for shunting. A medium-sized layout could be designed for that purpose, using a minimum of human resources.
A plan develops
I had seen some laser-cut layout boards by Grainge and Hodder at Narrow Gauge North, and thought they looked the part, being both strong and lightweight. Their range included traversers, which could combine the roles of turntable and fiddleyard. A pair could form either side of a U-shape, joined by boards containing the shunting yards. With careful planning of the track lines, there might also be room for some buildings. These I already had, loaned by Mike Lowe of Pendle Valley Workshop for use on Middleforth. The main problem was trying to fit too much track on too little board. A planning session on the lawn, using Mamod track and paint-pots to mark the corners, was instructive in that regard.
The Warley Exhibition was approaching, and I was awarded a pass to help run Monsal Dale, a 2mm layout built by Southport MRS. So one chilly November Saturday I took the train south to the NEC. The traverser makers had a stand there, so it was all too easy to place an order, thereby committing myself to another layout build. The final choice was three 1200 x 900mm boards and two 900 x 400mm traversers. A bonus was the expenses cheque from Warley MRC, right down to the weekend-rate parking at Wigan North Western.
Building baseboards
Just before Christmas, I unpacked the first of two large parcels. It was a work of art, over 100 plywood pieces in compact layers locked together by most of a roll of masking tape. If there is ever an award ceremony hosted by the Institute of Advanced Packaging, representatives of Messrs Grainge and Hodder will be on the front table, nervously awaiting the announcement of Best Rectangular Parcel in Cardboard 2016. Unpacking took some time, and when all out on the bench it resembled a giant 3D jigsaw puzzle. How it fitted together I hadn’t a clue.
Dismantling parcel No.2 revealed not only more intricately-interlocked woodwork but also instructions of the ‘Insert Tab A into Slot B’ variety. So over the next few days, and after a brief but intense session of Naming of Parts, I tabbed and slotted. I quickly realised that a shape in multiples of two, four or eight belonged to the traversers, whilst a part in triplicate or sextuplicate was identified with the main boards. The material itself was of high-quality three-ply, with a smooth slightly waxy finish pleasant to the touch.
As usual with laser-cut components, everything fitted together well, with only minor encouragement from a flat hand or a rubber mallet. I used PVA adhesive, with some joints clamped or weighted with lumps of metal while the glue set. I discovered an oddly-satisfying error in the instructions, in that Parts 9 (2 off) should be fitted to the top of Parts 2, not Parts 3. Fortunately Parts 9 would not fit in the wrong place, so disaster was avoided. Trying to unstick well-glued plywood joints did not bear thinking about.
Adding track and buildings
The next step was to test-fit the track and buildings. With a bit of jiggling a plausible layout appeared, with room for an engine-shed and a goods shed, in addition to existing buildings from Middleforth. A greenhouse and two permanent way buildings were also added to the shopping list. As it happened, I was due to participate in the Southport MRS’ annual pilgrimage to the Ravenglass and Eskdale Railway’s Track Week. This provides irresistible opportunities to hump sleepers, shovel ballast and excavate drainage ditches (without turning the water off). Supervision is provided by the foreman’s canine companions, with four well-planted paws and a hard stare being more than a match for any amount of their master’s random orders and arm waving. Generous tea-breaks in a heated mess coach and train-delivered hot lunches just add to the attraction.
The journey north passed Carnforth, so it was only a minor deviation to visit Mike Lowe’s emporium and order the additional buildings. Completion was promised in a fortnight or so, and duly delivered on time. The weight of the package was a little ominous - there was a lot of resin in both engine and goods sheds. After warming up on the greenhouse and a lamp room I took the plunge and started on the big ones. I rapidly discovered that slow and steady was the way to go, allowing the epoxy on one join to fully set before moving on. I added floors from plastic sheet, a fairly thick grade originally intended for bathroom suites. These would add strength when moving the buildings at exhibitions, and allow track to be fixed inside, using a layer of DIY filler as flooring.
After assembly to eaves-level and painting, the two buildings were set aside whilst the Mamod track was laid and scenery added. The track was painted brown for the sleepers and rust for the rail. I started with the left-hand turntable, as this had only one central connection with the main boards. This meant I could work on it in the relative comfort of the man-shed, without having to set up the layout in the garden to get all the joints right, in February. This board had a coal staithe and a stores hut, so most of the scenery was in shades of either grey or black, with a little scruffy vegetation struggling to survive. The side walls and paving slabs were made using filler in Jigstones moulds.
The adjacent main board was a touch crowded, with the goods shed, a ditto office, a PW hut and a two-storey cottage (complete with greenhouse and front-and-back gardens) all vying for space. It just fitted in, with railway and residential areas separated by a cocktail-stick-and-wire fence. The middle board was mostly track, with just a small signal cabin as the main feature.
The end board hosted the loco shed, a water tower, a line-side hut and a model shop, complete with an image of Mr Lowe firing a live steamer. It also had a diesel tank from a deconstructed Swift Sixteen tank wagon, resting on a Jigstones base and fitted with a fuelling hose made from an OO gauge waterwheel, O-gauge valves and plastic-coated wire, gauge unknown.
Scenery and testing
Some thought then went into ballasting options. Suitable materials were hard to acquire locally, and Derbyshire was a long way to go for the still-warm-from-the-crusher variety. Fortunately Swift Sixteen had some in stock, collectable from the Peterborough show, as if I hadn’t enough reasons to go already. The suggested coverage was about a metre of track per kilo, but I managed to make 4kg do the lot.
In late March a dry weekend saw the layout erected in the garden, resting on four metal trestles and a pair of purpose-made wooden legs for the turntable ends. Considerable progress was made, despite the clocks going forward and Mothering Sunday happening, also the season’s first operating day at West Lancs. A major milestone was a thorough fettling of the track, including getting both turntables to rotate smoothly. A trial run with an 0-6-0 Kerr Stuart diesel was successful, despite doubts as to whether the fully-flanged all-driven wheelsets would cope. The steamers tended to catch the point levers, so most of these had to be cut down to track level.
Another three weeks or so saw the boards coated with sand and painted to represent unmade ground around the sidings, with paved footpaths laid amongst scattered vegetation. The engine and goods sheds were roofed, and fitted for large plastic boxes in anticipation of transport to exhibitions. Then it was the Peterborough show, with many other layouts to provide inspiration and much swag to acquire, including some small wagons and loads.
The next issue was transport. A trailer languished in the garage, too small for the main boards but suitable for the turntables and assorted boxes. Ebay provided a new set of electrics, a cover and a big wodge of foam plastic as a shock-absorber for delicate models. Some varnish, well beyond its brush-by date, and some even older bitumen paint for the underside completed the job. To secure the layout for travel I made uprights from short lengths of planking to bolt the boards to, one above the other.
Southport’s Woodvale Rally was now approaching. Its attractions include a Railway Tent, whose coordinator is apt to sidle up a few weeks beforehand to enquire if I am ‘OK for the Show’. My response is to ask what type of layout is required. The invariable answer ‘What would you like to bring?’ is manna from heaven for any layout builder, and I had no trouble in having Kingsdown Roads accepted, sight unseen.
Detailing had now to be added, my favourite part of layout-building. A posse of Motley Miniatures figures made up the bulk of the workforce, most of them engaged in handling the crates, drums and parcels in and around the goods shed. These were a mixture of 3D-printed plastic and laser-cut wood items, including some I made all by myself.
To finish off, I needed some baseboard skirting. I rejected plain fabric material in a neutral colour for something more flamboyant, namely a set of five Kent County flags, in Post Office Red. Kent is the county of my upbringing, you may not be interested to know. Also of modest interest is the layout name, taken from a small village on the coast between Dover and Deal.
Public appearances
Woodvale came and went with no disasters. The layout behaved itself, as did the operators, and nothing fell off, always an important criterion for a successful exhibition. The transport concept also worked, which was a relief, even if the journey was fairly short. Some minor track adjustments were needed, but all-in-all the running was good-to-firm, as the racing fraternity say. Most loco movements were of the end-to-end variety, with occasional forays into the various sidings to pick or put down wagons, or just to get out of the way for a bit.
Next was the Corris Railway’s show at Machynlleth. This is a medium-sized event with a modest clientele and a friendly atmosphere that makes it enjoyable and stress-free. Whilst there I risked posting a photo on social media, to be rewarded within minutes by an invitation to the 2018 Peterborough show! I spent the rest of the day making a list of tweaks and upgrades, to ensure it would look and perform its best the following April. Afterwards my layout slaves and I awarded ourselves a leisurely Monday playing trains at the Lechlan Garden Railway at Twywn, a pleasing combination of woodland scenery and Peter Jones’ extraordinary industrial creations.
Back home, I felt the objective had been achieved and the ten months of designing and building had been well worthwhile. As for the lament in the title, it relates to a feeling that this may be my last Significant Project. Not so much Anno Domini, although I am apparently getting older every year, more that I have run out of garages and other storage space for layouts. So if anybody in the Southport area has some suitable real estate for rent at a bargain price, it could be good to talk.